Breaking down a bolt in an engine block can lead to a variety of issues. Even, a lack of skill in repairing can also cost you both time and money in hiring a professional for this simple task.
Learning how to drill out the broken bolt in engine block can save all your investment and let you continue your repair task without any interruption.
Following, we’ve shared a simple yet extremely useful step-by-step method for drilling out the broken bolt in the engine block, as well as some tips for removing other types of damaged bolts.
How To Drill Out Broken Bolt In Engine Block?
Drilling out a broken bolt in an engine block can be a daunting task for a technician, particularly if the bolt is too small. The typical method includes drilling a pilot hole, creating a center point on the broken bolt, hammering, and trying to take it out.
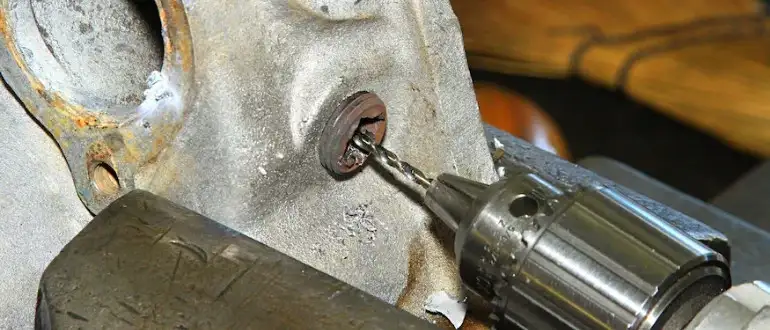
However, drilling out is one of the easiest ways to get the job done efficiently. Here is the step by step guide:
Choose the correct size drill bit
You should start with a smaller sized drill bit, like 1/8 inch, to prevent breaking bolt fragments. Then you can slowly enlarge the drill bit size.
Specifically, the IRWIN Screw Extractor will be the best drill bit set for this task. You can also use the DEWALT Titanium Drill Bit Set as it is the best value product.
Prepare the drill
A left-handed drill is preferable to drilling out a broken drill bit in the engine block. It’s also handy for creating a hole in the center part of the broken bolt. Keep the speed setting of the drill very low and set the drill to reverse mode.
Drilling out broken bolts doesn’t require high drilling speed. The drilling torque in reverse will protect the bolt’s threads and loosen the grip of the screw quite efficiently.
Create Pilot Hole
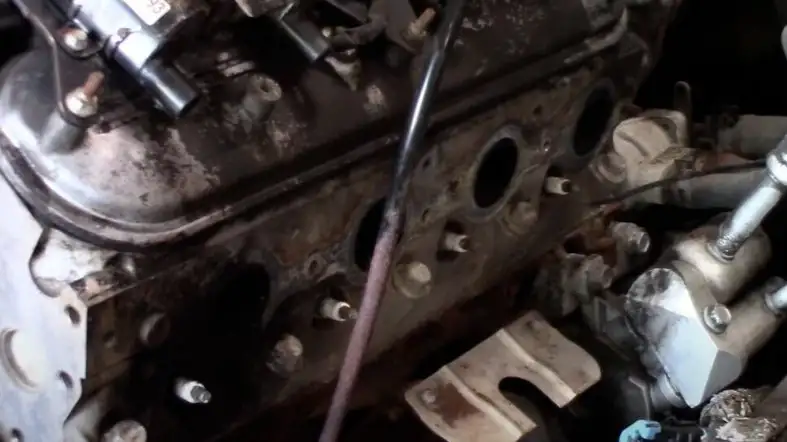
To drill out a broken bolt, you must create a hole at the dead center of it. So, punch apart the broken bolt and create a pilot hole. Drill as much as possible so you can set the next large size in the hole.
Drilling out the broken bolt
After creating the pilot hole, set the drill to reverse mode. Keep the drill speed at around 20 RPM and start drilling out into the hole.
Make sure you are drilling out gently on the broken bolt to avoid new issues. Change is that it can break the bolt, which will only exacerbate the situation.
While drilling out, the broken bolt should hold onto the drill bit and start coming off.
Keep drilling out at a slower speed until the whole broken bolt comes off completely. You can also allow a magnet to remove any metal shavings that may exist there.
Common Difficulties Experienced While Removing A Broken Bolt
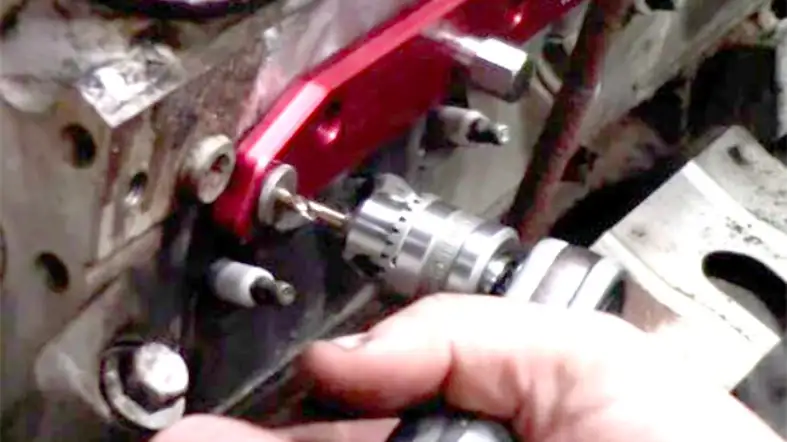
How to drill out a broken bolt in an engine block when there are extra difficulties that will make the process challenging? The following are a few potential obstacles and their solutions.
Stiff Broken Bolt
To remove a stiff broken bolt, mechanists mostly use an advanced grip technology tool. A broken belt can cause stiffening due to getting rusty or becoming older.
However, you can easily remove it by creating a center point or hole. It will significantly reduce the effort and let you remove the damaged fastener eventually.
Snapped or Worn-out Bolt
Snapped bolts are those that have been severely broken and damaged. These are more daunting to take out. However, plenty of extraction kits will let you do so conveniently.
These extraction kits drill a center hole in the bolt and remove it from the system.
You can also remove the extra metal particles from the hole using these kits. But you must pay extra attention while using any extraction kit as it can damage the engine parts while removing worn-out or snapped bolts.
Seized Bolt Without A Head
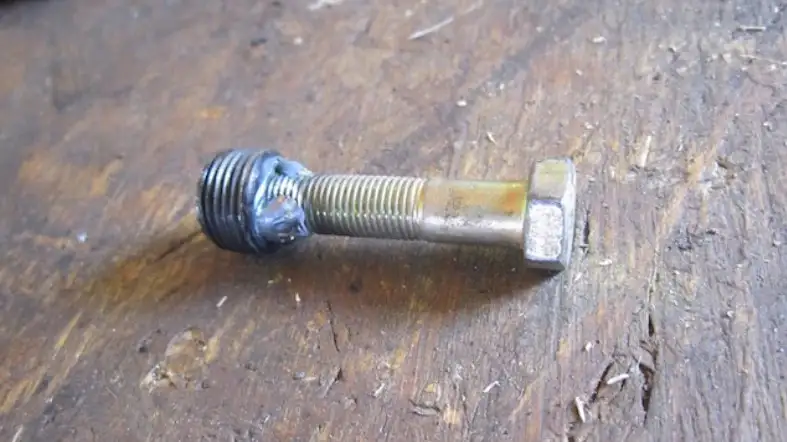
Removing seized bolts that don’t have a head is a most daunting task, amongst others. You can lose the bolt head if you use the wrong tool with excessive pressure to tighten it.
To solve this problem, you must loosen the seized bolt first. Then apply some lubrication to the bolt and allow the bolt to free up.
Then punch at the midpoint of the seized bolt using a center punch. Drill a center hole in it with a left-handed drill and you should be able to remove the bolt easily.
Make sure you are drilling a hole at a low speed. If the drill doesn’t work, apply the extraction tool.
Limitations to Access
Working in a tight space is always frustrating, and removing the broken bolt from such a spot can test your patience.
Sometimes you may need to remove a damaged fastener from deep space. In this case, you should apply a systematic approach using special tools.
A smaller drill bit can come in handy to let you create a pilot hole. Then you can apply the extracting tool to complete the rest.
FAQs
How To Remove A Broken And Rusted Bolt?
A rusted, broken bolt is tricky to get access to due to its rust. So your first task is to remove the rust by applying some hydrogen peroxide. It’s an effective method to dissolve the rust.
Clean the bolt surface using a hard brush and the whole remaining rut. It will loosen the bolt slightly, making the job easier. Now hammer the bolt and finally apply an extractor to remove your rusted bolt.
How To Remove A Broken Bolt From An Aluminum Block?
Apply WD-40 or Mystery Oil on the surface around the bolt head. After a moment, the lubricant will automatically penetrate into the threaded sections.
Wait for 3 to 4 hours until the lubricant entirely penetrates into the broken part and makes it lose, so you can remove it efficiently.
Final words
Hope you have an understanding of how to drill out the broken bolt in the engine block.
However, it’s not the only way to remove the damaged fastener as you can punch or drill the center of the bolt, weld it, or extract it to remove it from the engine block.
But drilling out is quite an effortless yet effective process to apply, especially for novice DIYers. However, the process takes lot of patience because faster or higher speeds can exacerbate the situation.